Three good reasons to install MOTOR SPEED DRIVES
First,
Motor Speed Drives will lower and may possibly eliminate your utility
demand charges because they offer built-in soft-start capabilities. This means
there will be no inrush current and no voltage sag effect on the rest of the
system.
Secondly,
we install Drives of the Pulse Width Modulation (PWM) type only, with a
diode converter front-end. By installing Drives of the PWM type only, the
Displacement Power Factor is high (commonly > 95 % at rated load) and more or
less constant throughout the range. This means that drives can reduce energy
usage and correct for DPF at the same time. It’s a good thing too, because
drives and PF correction capacitors don’t mix. Caps are vulnerable to the
higher frequency harmonic currents generated by drives, since their impedance
decreases as frequency increases.
Third,
Significant electrical energy
savings.
Even a small reduction in speed can give significant savings. For
instance, a centrifugal pump or fan running at 80% speed consumes only half of
the energy compared to one running at full speed.
How to cut energy consumption by nearly 50%
A centrifugal pump or fan running at half speed consumes only
one-eighth of the energy compared to one running at full speed. This is because
the torque needed to run a pump or fan is the square of the volume. For
instance, reducing the pump speed to 80% only requires 64% of the torque
(0.8x0.8). Furthermore, to produce 64% of the torque only requires 51% of the
power (0.64x0.8), as the power requirement is reduced in the same way.
The explanation for this lies in the pressure difference across the impeller.
When less pressure is produced, less acceleration of air or fluid across the
impeller is required. It is the simultaneous reduction of acceleration and
pressure that multiplies the savings.
High efficiency
Comparing energy consumption of various mechanical and electrical
airflow control methods of a typical centrifugal fan reveals that: At 80%
airflow, the energy consumption is: 97% of maximum with damper control; and 76%
of maximum using guide vanes; but only 51% using motor speed drives. The
difference between these figures represents wasted energy.
Low motor losses
The voltage to frequency ratio is automatically adjusted to
achieve optimum current for pump and fan loads. This minimizes motor losses and
reduces motor noise.
Low running costs
With 50% airflow, the commonly used guide vane system results in
the fan motor using over three times the energy (kWh) of a motor controlled by a
variable speed drive. These extra running costs, compared to inverter control,
are a powerful argument in favor of selecting a variable speed drive.
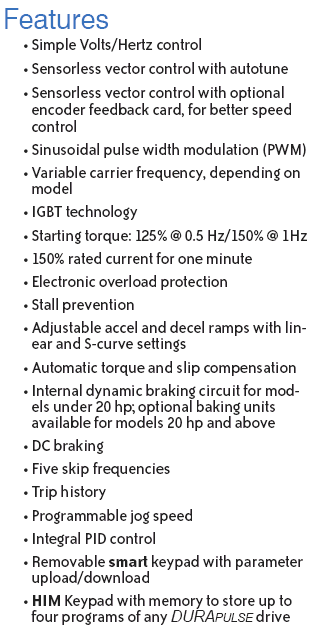
We install Line Reactors on the line side (Input) as well
as the load side (Output).
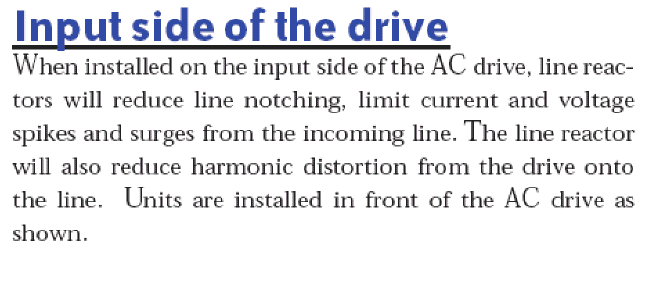
Input line reactors protect the
AC drive from transient overvoltage conditions, typically
caused by utility capacitor
switching. The input line reactor also reduces the harmonics
associated with AC drives.
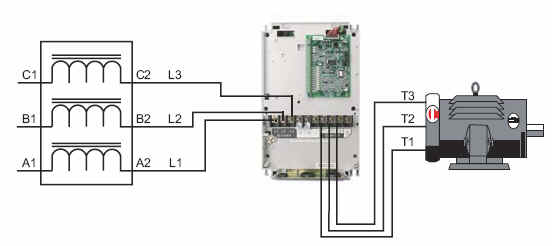
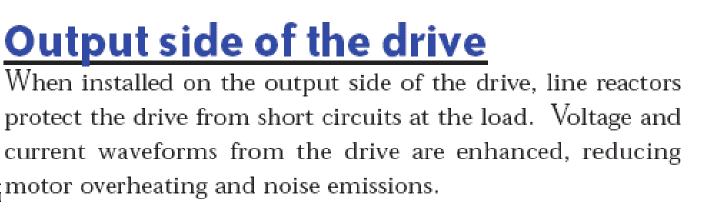
Output line reactors protect the
motor insulation against AC drive short circuits and
IGBT reflective wave damage, and
also “smooth” the motor current waveform, allowing
the motor to run cooler.
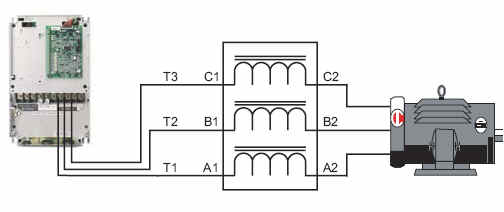